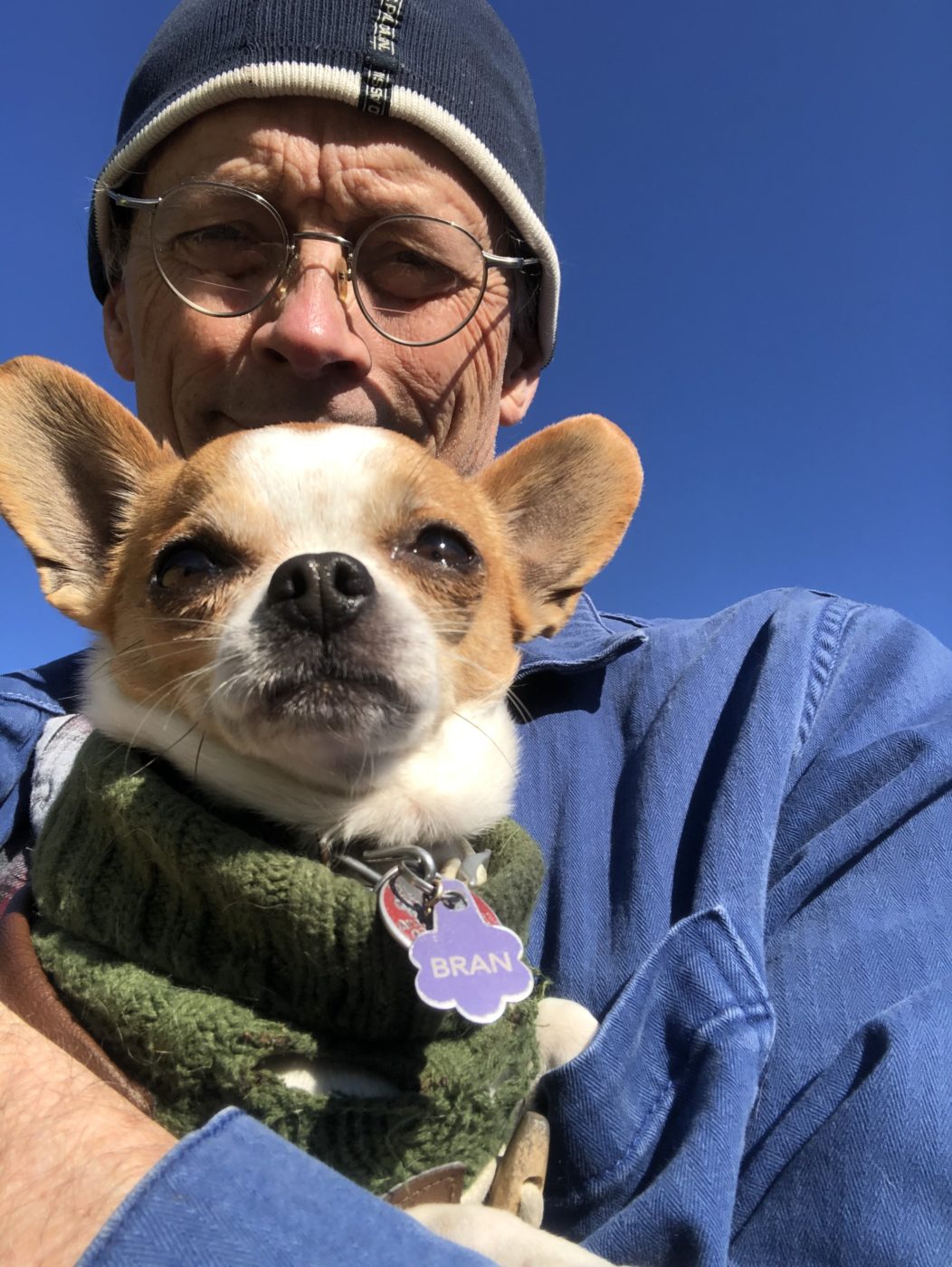
Image courtesy of Hank Murta Adams.
Hank Murta Adams
Artist Hank Murta Adams (1956– ) earned a BFA in painting at the Rhode Island School of Design (RISD) in the 1970s. Adams took glass classes there with Dale Chihuly before graduating in 1978, and he later studied glass at both the Penland School of Craft and Pilchuck Glass School. Adams has served in various roles while working as an independent artist, including as design director at Blenko Glass Company in Milton, West Virginia (1988–94) and as creative director at Wheaton Arts and Cultural Center in Millville, New Jersey (2003–18). Adams, who maintains his own studio in upstate New York, is particularly known for his rough, figurative sculptures.
Works
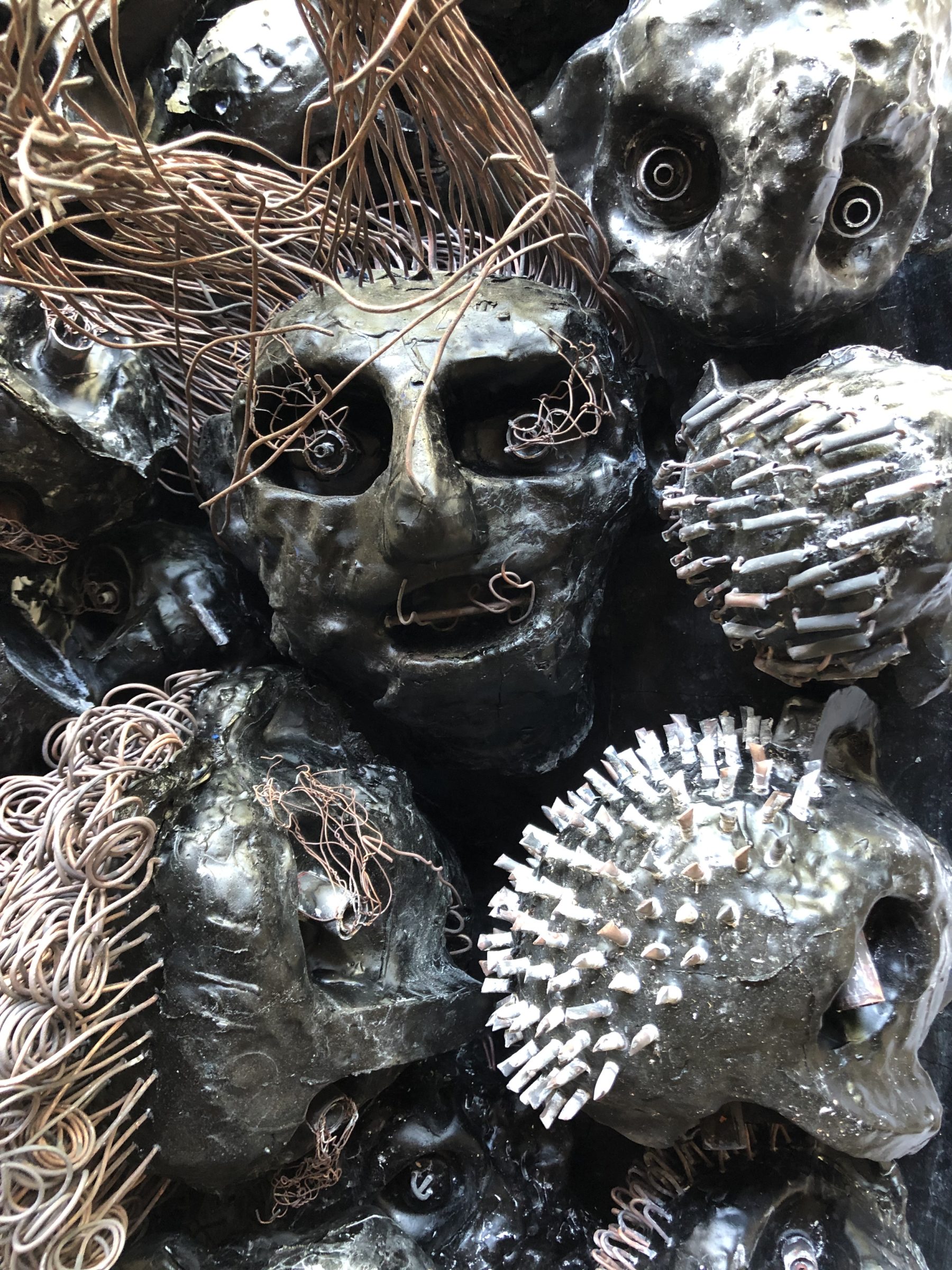
Work in progress (detail), 2020. Black glass. Image courtesy of Hank Murta Adams.
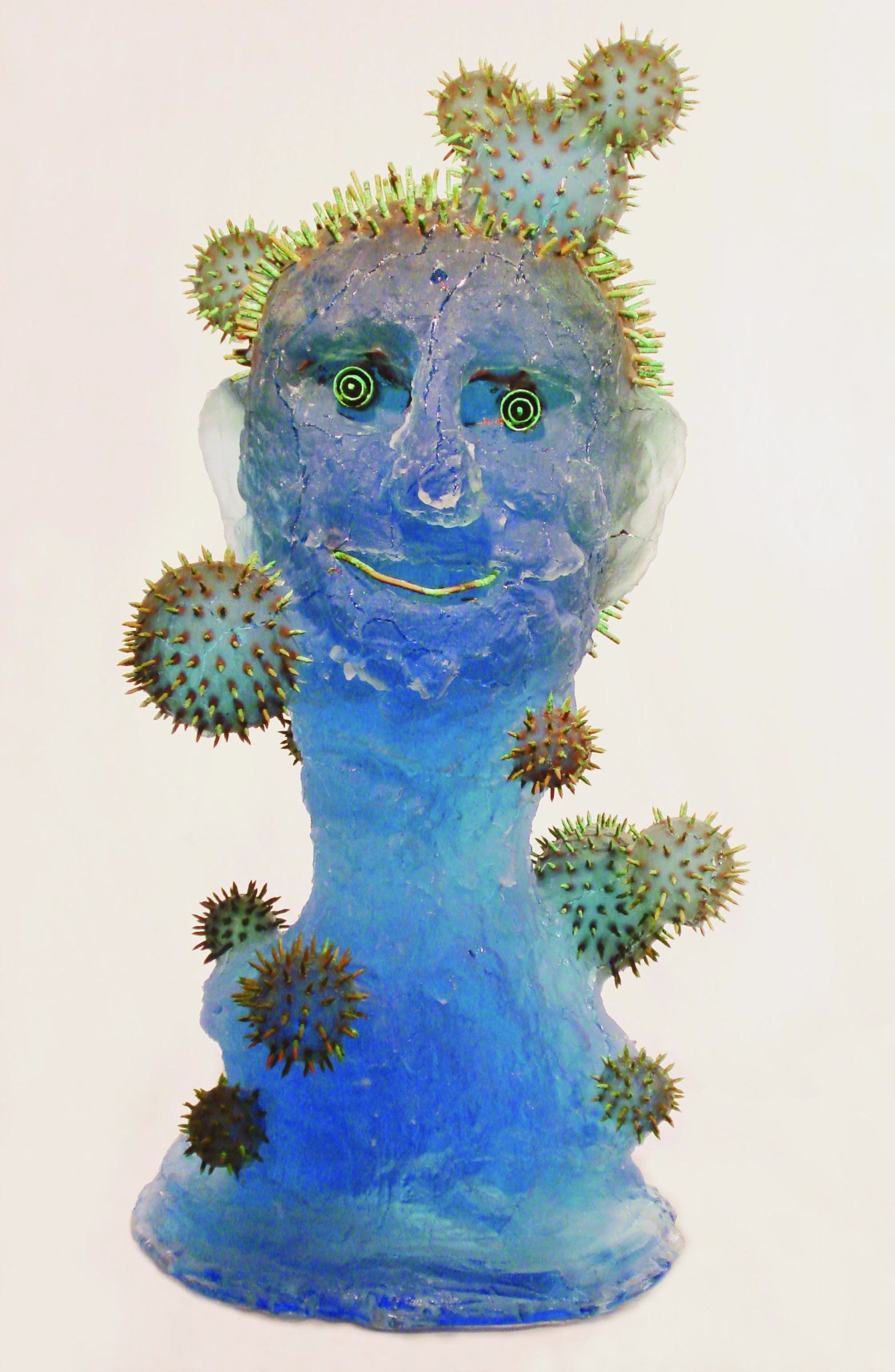
Nosher, 2006. Cast at Blenko Glass Company. Glass, copper. H: 33.5 in, W: 18 in, D: 18 in. Image courtesy of Hank Murta Adams.
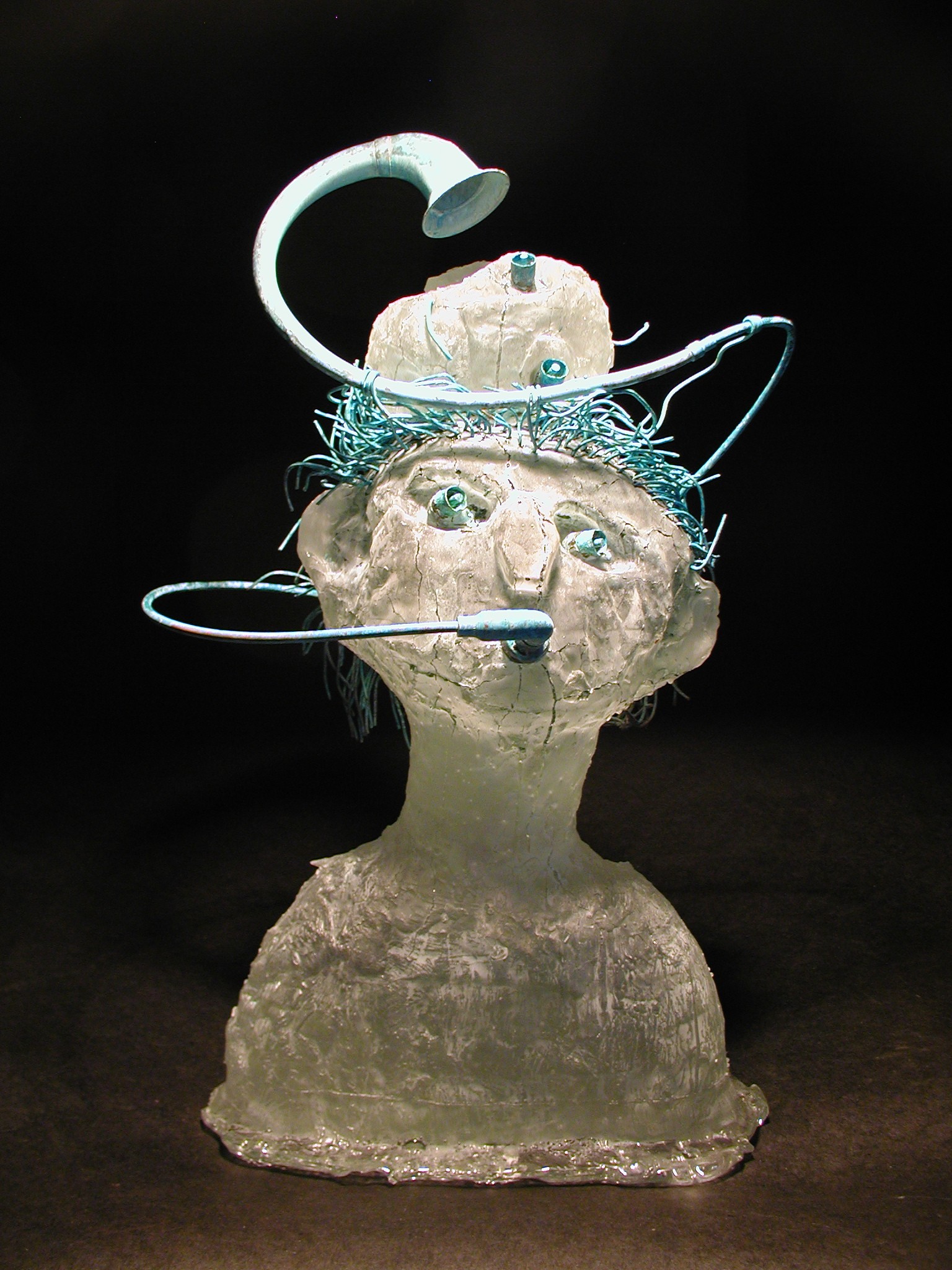
Gossipbater, 2005. Cast at Blenko Glass Company. Glass and copper. H: 30 in, W: 17 in, D: 17 in. Image courtesy of Hank Murta Adams.
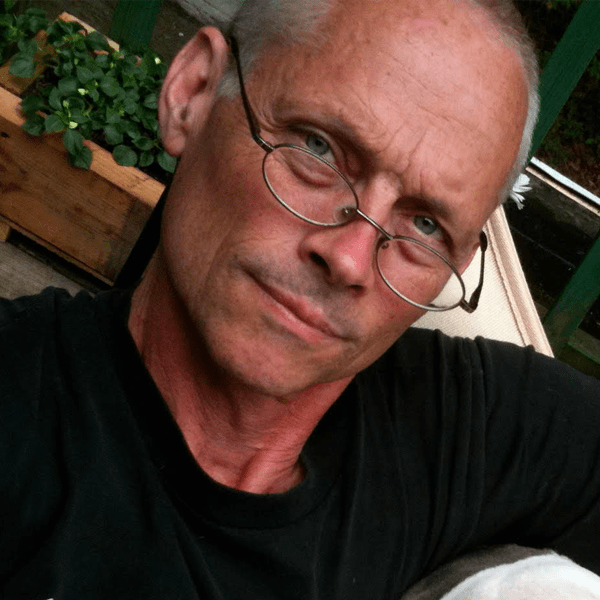
Hank Murta Adams talks about Blenko’s solid color glass and “upping” the choices.
Playing02:00 TranscriptHank Murta Adams talks about Blenko’s solid color glass and “upping” the choices. Oral history interview with Hank Murta Adams by Barb Elam, conducted via telephone, June 7, 2019, Bard Graduate Center. Clip length: 02:00.
Hank Murta Adams: The whole system in the modern glass movement is basically coatings of color from what started as Kugler but has now moved on to these companies that are many more, and much more variety of color, but it’s all potent color that’s been put on the end of the blowpipe and then you have a coating, inside coating, or with an overlay—an outside coating—of a higher density of glass that’s been blown out, and so you’re basically tinting a piece of glass. Well, the way the factories were working is that you had a whole furnace of a color of glass, and so the glass would be that color glass all the way through it, instead of a coating. So having that old system was—and it shows, I mean you look at a Blenko catalog and it’s just beautiful color, and it’s highly saturated, gorgeous color. Well, those are solid glass color—they’re not a coating. And no one knows that consciously, but their mind tells them that when they see it visually. So I had all this color system there, and so what I did is, to get more than—I forget, I think it was six colors they’d run a year, I can’t remember what it would be; six or seven—and we’d design a new color and phase one out—it would be the year of that color would be—we’d call it that—avocado, or whatever that year was—amethyst. And what I did is I upped the choices, which was kind of disastrous for the company as far as like having to manage it, but what I did is I would take, say a topaz, a yellow-transparent, or gold color, and I would coat it with an emerald, so you would then get a combination of those two. And what was really cool was that it would make the glass even more alive because when you’re blowing a piece of glass that is a half-topaz, yellow, and half-emerald green, but you blow it out, it actually is not even, it does a gradation—a slow gradation or a vibratory thing, which makes the glass extremely alive.
PermalinkHank Murta Adams describes Blenko as a living museum. Oral history interview with Hank Murta Adams by Barb Elam, conducted via telephone, June 7, 2019, Bard Graduate Center. Clip length: 01:21.
Hank Murta Adams: I taught in Detroit in 1987 and ‘97, but all through there I—and I taught at Cranbrook [Cranbrook Academy of Art, Detroit, Michigan], I taught a lot in the Detroit area, and I took—field trips of students down there often. And my students would just drop their jaw when they’d walk in, I mean it’s just such an astounding place—all the iconography, all the tools, they had no money so you’d pick up a monkey wrench and it would be—I mean, I wish I’d kept better notes, I wish I’d took more photographs—you’d pick up a monkey wrench and it would be repaired like seven times, braised with brass. And instead of buying a new monkey wrench for 20 bucks they would just fix it. They had a welder that looked like the—what’s the name of the first nuclear bomb? It looked like the main seal of a nuclear bomb. I’ll bet you they still have the thing. It was like the first welder ever made, and I mean welding technology changes every six months and this thing was from the thirties. I mean, it was just like, that’s—the whole place had just layers and layers and layers of such beauty, of such—the whole place was a museum.
PermalinkHank Murta Adams reminisces about Blenko’s workers. Oral history interview with Hank Murta Adams by Barb Elam, conducted via telephone, June 7, 2019, Bard Graduate Center. Clip length: 01:49.
Hank Murta Adams: [laughs] And the characters—oh my God. Paul Bowers was the night guard—Paul Bowers looked like the hunchback of Notre Dame, and Paul Bowers would chew what’s called plug. It’s not chewing tobacco, it looks like—it’s like a pepperoni of tobacco. And you slice off a piece of that pepperoni, you tuck it in your cheek, and you get a buzz for eight hours. Well, Paul Bowers had been chewing plug for so many years, his entire body was shaped around that—he looked like Louis Armstrong on that one cheek. His entire body was bent over and shaped into that cheek, ‘cause he’d been chewing it—and he was the nicest guy, and he would be cleaning the bathrooms, or just the sweetest guy, and he died in that plant, I believe. But I’ll just never forget the image, and I wish I had a picture of Paul Bowers. I wish I had a picture of him. There were so many characters. There were two glassblowers, I believe they were both blowers, not finishers, one was called ‘Radio’ and the other—and his brother was called ‘TV.’ [laughs] Those were their nicknames. I named a lot of my pieces after these guys, I think the Smithsonian [Smithsonian American Art Museum, Washington, D.C] has a piece of mine named Emzy [After Emzy Black]. That was the name of this big, big glass blower. And he was a relatively new guy there. And there was a big glassblower that was rather famous there named ‘Shorty’—he’s now passed on, but Shorty was a very short guy, very hardworking, very skilled, and he had just retired when I came in.
PermalinkHank Murta Adams talks about Blenko’s lamps and stoppered bottles and their popularity in the 1950s.
Playing00:46 TranscriptHank Murta Adams talks about Blenko’s lamps and stoppered bottles and their popularity in the 1950s. Oral history interview with Hank Murta Adams by Barb Elam, conducted via telephone, June 7, 2019, Bard Graduate Center. Clip length: 00:45.
Hank Murta Adams: I mean, I can spot a Blenko lamp in a second in an old photograph somewhere. I just saw one the other day and I was like ‘Ah, that’s Blenko.’ And you know, they were very famous for making their lamps, they were very famous for their stoppered bottle—their large stopper bottles—and, you know, they were showcased in the Museum of Modern Art [New York, New York]. I mean they were kind of the shit in the fifties. And all by, sort of like, default, by giving this faith and liberty to the designers, and then that feedback loop of designers having ego and pride—and Joel’s a [laughs] perfect example. Ego—he has a very big ego, and I love him for it.
PermalinkHank Murta Adams discusses Blenko in relation to other factories. Oral history interview with Hank Murta Adams by Barb Elam, conducted via telephone, June 7, 2019, Bard Graduate Center. Clip length: 00:35.
Hank Murta Adams: But yeah, I mean, the thing that really struck me about being living and working there—cause I would live down there, they had a little house for me—I was really struck by, you know—here’s—which is the way I viewed glass my whole life—is, ‘Okay. Here’s this myopia—here’s this focus. But what does that tell you about the periphery?’ I realized that this is just one factory telling a story because it’s still going, and it had some notoriety, but there were so many factories like that.
PermalinkHank Murta Adams describes how Blenko objects were produced. Oral history interview with Hank Murta Adams by Barb Elam, conducted via telephone, June 7, 2019, Bard Graduate Center. Clip length: 01:52.
Hank Murta Adams: You know, it’s such a small company, and there are people that should—there’s a guy named Dave Osburn who sort of became one of the lead gaffers there. The systems were so interesting and unique at Blenko; there would be two benches that would run production of a particular item, and the startups would be the blowers and they would have their team on one bench, and then there would be the finishers, and they would be—you have another team. So the piece would be started and if there were any color additions or bits that need to be—or dips need to be made on the start of the piece before it went into the mold, then it would be the blowers; and then it would be handed off to the team that were the finishers, and they would do the the lip wrap, and the opening up, and the finishing of the piece. Now, I don’t know if that was the way it was with all factories, but that’s certainly the way it was at Blenko, and when I landed there I know there were 140 people employed. As to how many—I think there were nine; nine teams on the floor as I remember, but, I might be wrong about that, but—and I can give you some names, but Bill Blenko—I think has passed, I’m not sure, I think he’s passed, but—and I can [laughs] tell you a lot about sort of the backstory of the company through the eighties and nineties and the aughts.
PermalinkHank Murta Adams explains how glass cullet is recycled. Oral history interview with Hank Murta Adams by Barb Elam, conducted via telephone, June 7, 2019, Bard Graduate Center. Clip length: 00:56.
Hank Murta Adams: And so the visuals that you sent me, I mean you show them to anybody and it’s like, ‘Wow, Candyland.’ So the reason for those bins, those outdoor bins, are because every glass factory utilizes a recycling of cullet and waste. So those bins are all separated because you can’t make a blue out of cadmium, and so those bins are all separated out so that they can reuse material and—for two reasons, it saves money, saves time, but it also helps in the melt. So that’s why the cullet yard, the picture’s of the cullet yard, which is right outside—it’s between the batch shed at Blenko and the main furnace, blow building—that’s where those pictures are taken.
PermalinkHank Murta Adams talks about cullet and remaining stocks of glass. Oral history interview with Hank Murta Adams by Barb Elam, conducted via telephone, June 7, 2019, Bard Graduate Center. Clip length: 02:00.
Hank Murta Adams: I’m getting work prepared for a show right now which is two specific colors, and there was a cullet supplier named [O.J] Gabbert in Marietta, Ohio. And he died several years ago, and it was bought by a farmer and he’s been selling off the stocks of what this whole conversation has revolved around, about these hundreds of plants that were in the Ohio Valley from the 1800s on. And this guy Gabbert would buy this cullet for nothing, or they would give it to him, and he would stockpile it in these bins, but he would market it to the glass scene. And so for years and years and years people were buying mostly—not glass from Blenko—Blenko might have been giving it away or selling some of it wasn’t their—they weren’t active and really active in doing it, it was sort of a buy thing. But for Gabbert, who was a dealer in cullet—and he was collecting mostly glass from Fenton, and that’s the glass that I’m using right now, and Fenton just—the building has been razed. Last year it was razed and all the stuff was auctioned off, so Fenton doesn’t exist anymore. The molds do, though, and I can tell you where a lot of them are [laughs], you know? So to the ‘cullet’ question—and I’ve, you know—this farmer that bought this—very nice guy and I know his staff and I was just there about three weeks ago, in Ohio, because I’ve been buying some of the late stocks of glass—and these are the final stocks and there—I can tell you right now, there’s no more yellow in this country from that era. And I don’t know if you know an artist named Amber Cowan, she’s young, she just had a show with Doug Heller—I think like her third show with Doug—very popular in the glass gallery scene now, and she does lampworking. And she has been using a lot of those old stocks as well, but they’re gone. I mean, her and I have the last stocks of them. So these cullets—and to me it’s a real—it’s another real hammer-blow in the coffin to—it’s the last of this industry, and it’s the last—you’re not even going to be able to buy the cullet anymore that were the remnants, the scrap remnants, of these factories. It’s gone.
PermalinkHank Murta Adams talks about the economics of labor and material after the second world war.
Playing0:49 TranscriptHank Murta Adams talks about cullet and remaining stocks of glass. Oral history interview with Hank Murta Adams by Barb Elam, conducted via telephone, June 7, 2019, Bard Graduate Center. Clip length: 02:00.
Hank Murta Adams: I’m getting work prepared for a show right now which is two specific colors, and there was a cullet supplier named [O.J] Gabbert in Marietta, Ohio. And he died several years ago, and it was bought by a farmer and he’s been selling off the stocks of what this whole conversation has revolved around, about these hundreds of plants that were in the Ohio Valley from the 1800s on. And this guy Gabbert would buy this cullet for nothing, or they would give it to him, and he would stockpile it in these bins, but he would market it to the glass scene. And so for years and years and years people were buying mostly—not glass from Blenko—Blenko might have been giving it away or selling some of it wasn’t their—they weren’t active and really active in doing it, it was sort of a buy thing. But for Gabbert, who was a dealer in cullet—and he was collecting mostly glass from Fenton, and that’s the glass that I’m using right now, and Fenton just—the building has been razed. Last year it was razed and all the stuff was auctioned off, so Fenton doesn’t exist anymore. The molds do, though, and I can tell you where a lot of them are [laughs], you know? So to the ‘cullet’ question—and I’ve, you know—this farmer that bought this—very nice guy and I know his staff and I was just there about three weeks ago, in Ohio, because I’ve been buying some of the late stocks of glass—and these are the final stocks and there—I can tell you right now, there’s no more yellow in this country from that era. And I don’t know if you know an artist named Amber Cowan, she’s young, she just had a show with Doug Heller—I think like her third show with Doug—very popular in the glass gallery scene now, and she does lampworking. And she has been using a lot of those old stocks as well, but they’re gone. I mean, her and I have the last stocks of them. So these cullets—and to me it’s a real—it’s another real hammer-blow in the coffin to—it’s the last of this industry, and it’s the last—you’re not even going to be able to buy the cullet anymore that were the remnants, the scrap remnants, of these factories. It’s gone.
PermalinkHank Murta Adams talks about the aesthetics of cullet. Oral history interview with Hank Murta Adams by Barb Elam, conducted via telephone, June 7, 2019, Bard Graduate Center. Clip length: 00:43.
Hank Murta Adams: Well, I think it’s human nature because they’re—yeah, they’re beautiful in the sunlight; it’s also, we’re of physical dimension, we are animals so we hoard and, I mean, what more could be—what more could be said about these big beautiful jewel piles and resources? So their tonnage of—I mean, to look at pictures is one thing, but to see that glistening in the light, and to see just the vastness of a resource is completely entrancing, and so, sure, anybody would pull their camera out for that stuff.
PermalinkHank Murta Adams discusses a piece he made as an ode to Blenko. Oral history interview with Hank Murta Adams by Barb Elam, conducted via telephone, June 7, 2019, Bard Graduate Center. Clip length: 00:47.
Hank Murta Adams: And I did a piece, actually, that’s in the Lowe Museum [Lowe Art Museum, University of Miami, Coral Gables, Florida] in Florida, that was really kind of an ode to, not just Blenko itself, but to sort of that era, and to why it died, and it’s a large installation piece that I exhibited a couple places; one was upstate New York at a non-profit art center. And collectors named the Palleys [Myrna and Sheldon Palley] who have the Palley Pavilion at the Lowe Museum—it’s part of the University of Florida—University of Miami [Miami, Florida]—they bought that piece and it’s on display in their glass collection, which is kind of an odd place for it but it does have glass in it. But it really was an ode to why that era died in America.
PermalinkHank Murta Adams discusses his role in producing the Blenko catalog. Oral history interview with Hank Murta Adams by Barb Elam, conducted via telephone, June 7, 2019, Bard Graduate Center. Clip length: 03:31.
Hank Murta Adams: There are two really interesting facts I’ll tell you quickly: one was that the catalog was completely shot on film, obviously, back then—and that some of the shots for this color catalog were hour long exposures for each shot. They’d set the camera open, and open the shutter, and leave cause it was shot on these four-by-four Kodachromes. And when you look at these catalogs, there’s just this beautiful—like when—you know, when you look at a Kodachrome slide, there’s just something that’s so—I mean, we think of it as authentic, but it’s not, it’s just a very saturated color, it’s just another reality. And then, towards the end of my tenure there, like, ’90, maybe ’93, I go up there to produce the catalog and I would have to go up—it’s like a two hour drive up there—two and a half hour drive up from Milton [West Virginia] on up to Williamstown and Marietta to the publisher, and I would have to get a—Blenko had a big box truck, so we’d fill that thing entirely up with all the samples to be photographed. And because you have all the samples produced in six colors and the colors are always, you know—the color tank—the colors aren’t always right; they go off. And so the time period between when the samples we’ve produced, and even the stocks of the lines that are staying in the line—the items that are staying in the line from years prior—you had to assemble all that so it could be rephotographed. So we’d get a big box truck, fill all with these samples and then I’d get up there and you start to assemble the stuff on the glass shelves for the catalog and the color’s wrong or the piece is made horribly—I’d have to drive up and down and get these things, and I’d spend, the week, or 10 days I’d be up there—I’d be up and down a bunch of timesI’d have to go back and then call the factory—and say, ‘You’ve got to make this in topaz.’ The sample we have is just impossible, I can’t even fake it in a photograph. So towards the end of my tenure I tell that to the photographer and the publisher comes in, he says, ‘Oh don’t worry about that, we now have these Japanese digital printers, and we can adjust that color for you.’ And I was like, ‘What do you mean, you can adjust the color?’ And this is the earl—this is in the early part of digitization, and I’m like, ‘What the hell are you talking about you can adjust the coloring of the—’ you know, I just was like—you know—honestly, I mean it’s just seems—I’m not that old and it just seems like it’s so archaic and such another era—and so sure enough, that year—and it’s in the beginning of it—and they were these brand-new—I remember they were Japanese printing presses and they were able to dial in the color, and so he said I didn’t have like a topaz piece, or whatever the hell it was, he says, ‘Don’t worry about it, we can make that emerald if you want.’ And I’m like—I just was like—it was—to me it was impossible. And so—but I was happy, I didn’t have to drive up and down to Milton all week, and so—but it also was kind of like—and it really struck me as an artist back then, I was like, well, you don’t even have to make the work then, you know, like which is what it is today; you don’t have to make the work—you can completely—but that matches in with this reality of this, you know this very human, this very physically exhaustive, this very present material. And that’s the way I teach it, I teach it as a teaching example, you know, and there aren’t—give 30 years from now that’ll all be completely the perspective of that—I’m not saying I’ll disappear, but there’s a time period in this country from the seventies to like the middle eighties—late eighties that really speaks to what you’re talking about, about the loss of even—it’s kind of like right in front of our faces, but disappearing.
PermalinkHank Murta Adams discusses being part of Chihuly’s community at RISD. Oral history interview with Hank Adams by Barb Elam, conducted via telephone, June 7, 2019, Bard Graduate Center. Clip length: 00:40.
Hank Murta Adams: Cause I was a student of Dale’s [Chihuly] at RISD [Rhode Island School of Design, Providence, Rhode Island] undergrad—I was a painter. I started to hang out with Dale’s ‘family,’ so to speak, and it was entrancing, and it was community, and it was also new. And so I completely embraced that, and the cast of characters that were there—and it was Howard Ben Tré, Toots Zynsky, Steve Weinberg—all those people within the ten years that Dale taught there were sort of—I was at the tail end, I think it was at year eight or nine there, I’m not sure. So it was very much a family and embracing for me.
PermalinkHank Murta Adams discusses the dissolution of the handmade industry in the Ohio Valley.
Playing01:36 TranscriptHank Murta Adams discusses the dissolution of the handmade industry in the Ohio Valley. Oral history interview with Hank Murta Adams by Barb Elam, conducted via telephone, June 7, 2019, Bard Graduate Center. Clip length: 01:36.
Hank Murta Adams: So I went from there, sort of by accident, to grad school, and didn’t do glass in grad school, but when I got out of grad school—and while I was an undergrad—it was really the beginning of the definite dissolution of the handmade glass industry in the Ohio Valley, and there were hundreds of these factories; and most of them had already sort of passed out, but there still were probably, I’m gonna guess—25, 20? But they were being sold off, auctioned off. The molds were being sent to scrap yards, and I’m a young kid and I’m just like, observing this, and I was younger than all those people I told you about—like Howard [Ben Tré], they’re all two to four years or maybe more older than me—but they were all my buddies and my friends and—so I’m of that second generation, but I’m younger. But I’m definitely out of that ilk. And so it was very interesting to sort of see, and as I’ve said in my lectures, my entire adult life has, sort of, seen the disintegration of hand-worked industrial revolution coming to a full closure, and the last gasps of it. And Blenko was very, very special within that.
PermalinkHank Murta Adams talks about Don Shepherd and Blenko. Oral history interview with Hank Murta Adams by Barb Elam, conducted via telephone, June 7, 2019, Bard Graduate Center. Clip length: 02:01.
Hank Murta Adams: Doug Heller knew I needed a studio, so he suggested that I call Don Shepherd who was the designer of Blenko. Now, Don was a very interesting character; he was an architect who lived in Connecticut and he—very seventies aesthetic—and I’m not sure exactly how he got into Blenko, but he had designed there for, like, 10 years at the time I met him. And he was looking to leave, and he would commute in from Connecticut. He was, as I said, an architect and a designer of—and glass was sort of accidental to him, except that he was making some very interesting work that Doug [Heller] was selling, and it’s—you might know it, it’s not very well known, though, but they were rea—and I was totally smitten to pieces. So Doug put us together, and he told me that Don was looking to cast because the oven that he was using was actually co-owned with him by Howard Ben Tré. And Howard Ben Tré, when he left RISD, he was looking for a place to cast. This was before he went into Brooklyn and even before he was casting in New York. So he had this oven built, it was built by a colleague of mine at RISD, named Greg Morell. And Greg built this very—we wouldn’t build them this way anymore, but it was a large oven for the time, and Don [Shepherd] didn’t know how to use it, or the computer that came with it, and so he was looking for somebody to sort of teach him. And so basically he offered me half ownership of that oven, and that was my entrance into the Blenko plant.
PermalinkHank Murta Adams recalls Bill Blenko inviting him to design for the company.
Playing03:32 TranscriptHank Murta Adams recalls Bill Blenko inviting him to design for the company. Oral history interview with Hank Murta Adams by Barb Elam, conducted via telephone, June 7, 2019, Bard Graduate Center. Clip length: 03:32.
Hank Murta Adams: And—I want to tell you, going into this plant was—it was just amazing. It was quite large, it was a very old—sort of a butler building was the main factory, and they had about 15 furnaces; some were anywhere from—at that time, they have smaller ones now, but at that time they had anywhere from two to, say, five tons were the furnaces. And those were ‘monkey pots,’ to what we would call ‘day tanks,’ which were the larger—the clear tanks were the larger tanks. So going in there and having—you know, I think there were at least, I’d say 90 people on the floor, all working. There’s nothing like that in this country at all, ever, again—handwork like that. So it was real—and it was just jaw-dropping, to go in there and watch that. And Blenko, they never really made a lot of money. They did have the most successful line, I think it was in—that I produced for them, was their record sales—were in, I believe, ‘93 or ‘94. And I worked real—you know, and I—we’re going back to how I got in there with Don [Shepherd], I started to use that oven and I started to cast all my own work there. I had unlimited use of the color. So I did that, and I was casting there, I can’t remember how many times; and then Bill Blenko—it was fairly soon though, Don had announced—Don Shepherd—had announced that he was leaving to them, and he never asked me if I wanted the job because he knew I was an artist, and, like, why would I want to do this. And he didn’t ask me. And then Bill Blenko called me, I was up in New York, and said, ‘Would you want to design for us?’ and I said ‘No, Bill. I’m not interested,’ and I let it go. And then he called me again in two weeks—and he said, ‘Please, would you please consider this?’ And so I thought to myself, ‘Well, how hard can it be to design glassware—I mean it’s all a history of shapes,’ and so I said, ‘Okay, I’ll do it,’ and I was thinking to myself, I knew I would get a carte blanche use of the place, but I really was not interested in designing for them. And so I agreed to do it, it was at half year point, and I said, ‘Well don’t expect much from the first year—the way the design year works.’ Even that is completely turned on its head now and doesn’t happen, not just in the glass world, but in the entire design world operated in that cycle of what happened at Blenko. And it was a—completely another culture to a kid that was a fine arts major and that [laughs] went to school for painting. And it was just like, my naivety, and my interest, and my curiosity was the blessing because I was just—I’m not going to say I wasn’t judgmental, or I wasn’t critical of things, but I kept my mouth shut and I was a student, and I was learning, and I was humbled every step of the way by these people that worked there were astoundingly hardworking. And so I was sort of self-interested, by getting my work done there and I did cast my work and I don’t know how I did it when they’d review because to do investment castings, which were called ‘unique molds,’ single shot, you lose it, you lose it, there’s no other molds—no record, my pieces would anneal for six weeks. They’re life size or larger, twice life-size, and I would make those molds in New York, I would truck them all the way down to West Virginia. I’d arrive at three in the morning, usually unload them myself, and get them into the oven so that I could cast them within three days and then be gone. And that’s what I did before I was officially designer.
PermalinkHanks Adams discusses being a designer for Blenko. Oral history interview with Hank Murta Adams by Barb Elam, conducted via telephone, June 7, 2019, Bard Graduate Center. Clip length: 01:54.
Hank Murta Adams: I was the seventh designer for Blenko, and the really interesting thing to me is that there was always this respect, and this sort of aura of, quote, ‘the designer.’ There was only one designer at a time, I was the seventh, and there was a complete respect for the job and the person doing that, although they would tease the hell out of you and run you through the ringer and—but Blenko—it’s a very fascinating—and it’s actually taught me a lot in my career in non-profit and in teaching. They gave, kind of, quite a liberty to us, and as with me. And I wasn’t disdainful of it, just like, ‘Well, how hard could it be to do this? You do these shapes, and give them to the teams to make, and then they do them.’ Well, I soon realized that I had 140 families that I was responsible for their livelihood and for the company, and the longer that I was there, the more that I just sort of observed this incredible piece of history. I took it more and more seriously, and more in earnest, and yet the company was falling apart. It had no money. It was a very bizarre situation. But as I cared for the men, and as I engaged with the men—and this is when I stopped blowing glass. I started to phase the casting, but I really stopped blowing glass there because I wasn’t going to get into a competition with these dudes cause I [laughs] wasn’t that orthodox a glassblower, and it was like, ‘This isn’t my job. I’m here’—and so it became more European, which is very different than Joel Myers, and very different from some of the others; closer to Winslow Anderson, and closer to a few of the others that were not actually hands-on. But the trick with me was that I had blown glass for 10 years so they couldn’t get anything by me.
PermalinkHank Murta Adams discusses the work environment at Blenko. Oral history interview with Hank Murta Adams by Barb Elam, conducted via telephone, June 7, 2019, Bard Graduate Center. Clip length: 01:58.
Hank Murta Adams: I mean it was really hard labor; they would start at six in the morning, and it was really intensely difficult work with—there was a guy who was the foreman named ‘Jarfly’ and he was there most of my tenure, he left while I was there. But he was there most of the time, and Jarfly was the bull that ran the entire studio, and everybody kissed Jarfly’s ass and Jarfly was a hard-ass, and Jarfly was also very loving to the guys. It was very interesting to watch him. And so I had to engage with all these different levels, and I had basically had to win these guys over. And when I first started at Blenko I took over from Don [Shepherd]. Basically, I would come in, I would make molds, we would prototype when I’d get up with them early in the morning, at six in the morning I’d start; and we would start prototyping and running samples and molds and work ideas out—test out—very hard work, intensely hard for me because I had to teach them, I had to show them new things, I had to coax them. And I came there and they—when I first started, I asked them to put a lip wrap on something, they’d spit at my feet. And I just—you know, it’s like, I took it, and—so it didn’t take more than six months before they realized that I cared about them and I was intensely caring about the product and the work, and so through my criticism—and boy, [laughs] I did criticize them, but they loved me for it, because they weren’t getting anything. And so I’d come in from New York, on my trips, and first thing I’d do is I’d go to the lehr—the moving lehr—the work would be coming off the belt, and I would look at all of the pieces that had been recently designed, on production, and accepted into the line, and they’d be horribly off. And I would put them on a cart and I’d tell the lehr boy to take these and go chuck them in the pond. Well, that certainly caused a sensation.
Permalink