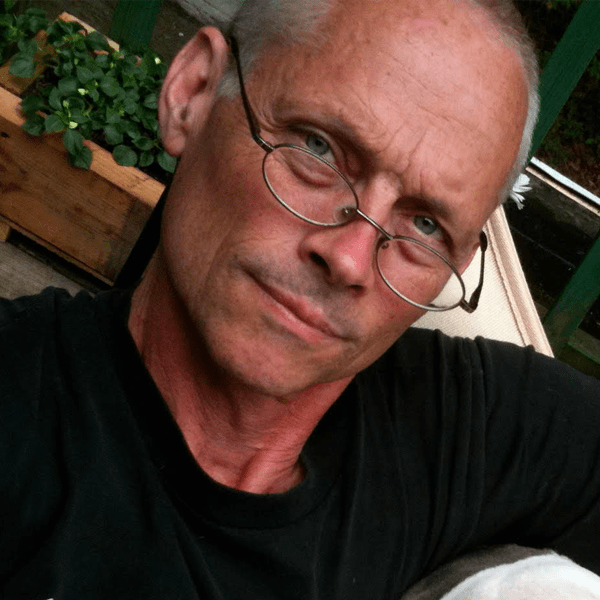
Hank Murta Adams recalls Bill Blenko inviting him to design for the company.
03:32Hank Murta Adams recalls Bill Blenko inviting him to design for the company. Oral history interview with Hank Murta Adams by Barb Elam, conducted via telephone, June 7, 2019, Bard Graduate Center. Clip length: 03:32.
Hank Murta Adams: And—I want to tell you, going into this plant was—it was just amazing. It was quite large, it was a very old—sort of a butler building was the main factory, and they had about 15 furnaces; some were anywhere from—at that time, they have smaller ones now, but at that time they had anywhere from two to, say, five tons were the furnaces. And those were ‘monkey pots,’ to what we would call ‘day tanks,’ which were the larger—the clear tanks were the larger tanks. So going in there and having—you know, I think there were at least, I’d say 90 people on the floor, all working. There’s nothing like that in this country at all, ever, again—handwork like that. So it was real—and it was just jaw-dropping, to go in there and watch that. And Blenko, they never really made a lot of money. They did have the most successful line, I think it was in—that I produced for them, was their record sales—were in, I believe, ‘93 or ‘94. And I worked real—you know, and I—we’re going back to how I got in there with Don [Shepherd], I started to use that oven and I started to cast all my own work there. I had unlimited use of the color. So I did that, and I was casting there, I can’t remember how many times; and then Bill Blenko—it was fairly soon though, Don had announced—Don Shepherd—had announced that he was leaving to them, and he never asked me if I wanted the job because he knew I was an artist, and, like, why would I want to do this. And he didn’t ask me. And then Bill Blenko called me, I was up in New York, and said, ‘Would you want to design for us?’ and I said ‘No, Bill. I’m not interested,’ and I let it go. And then he called me again in two weeks—and he said, ‘Please, would you please consider this?’ And so I thought to myself, ‘Well, how hard can it be to design glassware—I mean it’s all a history of shapes,’ and so I said, ‘Okay, I’ll do it,’ and I was thinking to myself, I knew I would get a carte blanche use of the place, but I really was not interested in designing for them. And so I agreed to do it, it was at half year point, and I said, ‘Well don’t expect much from the first year—the way the design year works.’ Even that is completely turned on its head now and doesn’t happen, not just in the glass world, but in the entire design world operated in that cycle of what happened at Blenko. And it was a—completely another culture to a kid that was a fine arts major and that [laughs] went to school for painting. And it was just like, my naivety, and my interest, and my curiosity was the blessing because I was just—I’m not going to say I wasn’t judgmental, or I wasn’t critical of things, but I kept my mouth shut and I was a student, and I was learning, and I was humbled every step of the way by these people that worked there were astoundingly hardworking. And so I was sort of self-interested, by getting my work done there and I did cast my work and I don’t know how I did it when they’d review because to do investment castings, which were called ‘unique molds,’ single shot, you lose it, you lose it, there’s no other molds—no record, my pieces would anneal for six weeks. They’re life size or larger, twice life-size, and I would make those molds in New York, I would truck them all the way down to West Virginia. I’d arrive at three in the morning, usually unload them myself, and get them into the oven so that I could cast them within three days and then be gone. And that’s what I did before I was officially designer.